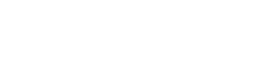
Mr. Zhang
Leave a messageHot die forging press widely used in the mechanical industry, meanwhile the beam is an important part of the hot die forging press equipment. Its quality will directly affect the operation and production efficiency of the customer's equipment. we have a wealth of experience in large steel casting, and the production of hot die forging press lower beam is favored by customers.
Specification:
Weight:> 5-80 Ton
Material:ZG35, ZG45, etc
Application:Forging\ Metallurgy industries
Customizable: Yes, according to customer's drawings
Our Advantages:
1.Rich experienced, capable of mass production of hot die forging upper and lower beams and other components, with short casting cycle;
2.During the casting of hot die casting beam steel casting, we strictly controls the sample testing, product inspection, quality assessment and other work of raw materials, and equipped with German OBLF company GS1000 vacuum direct reading spectrometer, carbon sulfur high-speed analyzer, digital ultrasonic flaw detector, multi-purpose magnetic powder flaw detector and other professional physical and chemical testing facilities. Non-destructive testing of each casting products, do not let defective products leave the factory;
3.Adopt modification treatment and ladle bottom blowing argon technology to strictly control the quality of liquid steel, efficiently reduce the content of gases and harmful elements in liquid steel, improve its purity, so as to ensure that the quality of hot die forging press beam to meet customer requirements.
Casting accuracy:
According to Č SN 014470, it is classified as 4-5 levels, or according to DIN 1683, it is classified as GTB 17-20 levels
Heat treatment of castings: 1. Fire to eliminate internal stress; 2. Normalization and tempering; 3. Quenching and tempering
Casting processing: 1 Rough machining is carried out at the customer's site with a margin for precision machining; 2. Perform final processing according to the drawings
Inspection before delivery of castings: 1 Chemical analysis; 2. Mechanical testing; 3. Size agreement; 4. Conduct ultrasonic, coloring, or magnetic particle surface testing as required
We are a leading open die & closed die forgings and castings parts supplier, we produce rough machined, semi-finished, and finished parts and fabricated assemblies for demanding applications.
Copyright (C) 2024 Wuxi Jieshengyuan Machinery Co., Ltd. All rights reserved
Site map
Comment
(0)