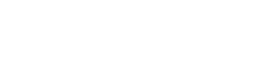
Mr. Zhang
Leave a messageThe bearing seat is an important component for fixing bearings and ball mills, mainly bearing the entire weight and impact force of the cylinder, and playing a supporting role in the entire bearing component. Where there are bearings, there must be support points. The inner support point of the bearing is the shaft, and the outer support is commonly referred to as the bearing seat. The quality of the ball mill directly affects its production efficiency and equipment operation safety.
Advantages:
1. The bearing seat operates for a long time in an environment with low-speed heavy load and impact, so it needs to have high strength and wear resistance, and requires a certain degree of shock absorption performance.
2. The bearing seat is cast using high-quality steel such as ZG35 and ZG45, which have high hardness, wear resistance, strong load-bearing capacity, can work continuously for a long time, good stability, and long service life.
3.The bearing seat is lubricated with thin oil, which reduces the friction coefficient of the bearing to a smaller value, has good energy-saving effect, and the normal operating temperature of the bearing is much lower than that of dry oil lubricated bearings, extending the service life of the bearing.
4.The lower seat of the bearing is equipped with an oil level observation oil gauge, which can be used to check the oil level at any time and replenish the oil in a timely manner, preventing poor lubrication due to lack of oil and avoiding bearing damage accidents.
5.Removing the outer top sleeve of a compressed bearing prevents dust from entering the bearing box, maintains good oil quality, ensures the service life of the bearing, and ensures safe and reliable operation.
Heat treatment of castings: 1. Fire to eliminate internal stress; 2. Normalization and tempering; 3. Quenching and tempering
Casting processing: 1 Rough machining is carried out at the customer's site with a margin for precision machining; 2. Perform final processing according to the drawings
Inspection before delivery of castings: 1 Chemical analysis; 2. Mechanical testing; 3. Size agreement; 4. Conduct ultrasonic, coloring, or magnetic particle surface testing as required
We are a leading open die & closed die forgings and castings parts supplier, we produce rough machined, semi-finished, and finished parts and fabricated assemblies for demanding applications.
Copyright (C) 2024 Wuxi Jieshengyuan Machinery Co., Ltd. All rights reserved
Site map
Comment
(0)